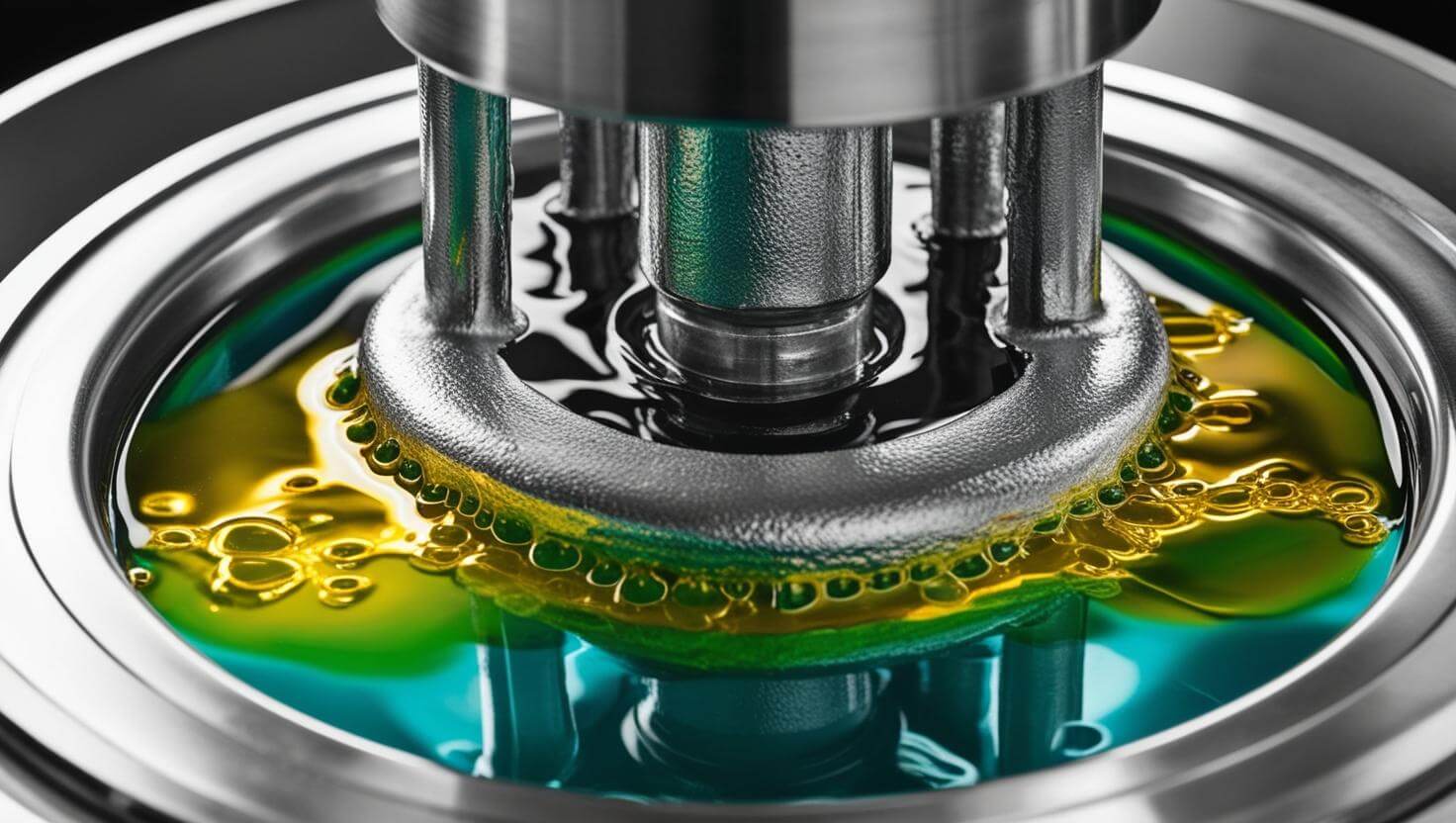
Wer denkt, 3D-gedruckte Teile aus Kunststoff seien nur für einfache Prototypen oder geeignet, hat Galvanisieren bisher nicht entdeckt. Denn mit diesem Verfahren lassen sich 3D-Drucke nicht nur optisch veredeln, sondern auch funktional aufwerten. Der folgende Artikel erklärt, wie das Galvanisieren von 3D-gedruckten Teilen funktioniert, für wenn es interessant ist und welche Möglichkeiten es bietet.
Was bedeutet Galvanisieren?
Galvanisieren, auch als Galvanotechnik oder Elektroplattieren bezeichnet, ist ein elektrochemischer Prozess. Bei diesem Verfahren wird eine Metallschicht auf ein leitfähiges Substrat aufgebracht. Dabei wird das Objekt in ein elektrolytisches Bad getaucht, in dem es als Kathode fungiert. Die Anode besteht aus dem Metall, welches auf die Oberfläche aufgetragen werden soll. Durch das Anlegen einer elektrischen Spannung wandern Metallionen von der Anode zur Kathode und bilden dort eine gleichmäßige Schicht.
Dieser Prozess unterscheidet sich von der Galvanoplastik, bei der eine Form beschichtet und anschließend entfernt wird. Dadurch entsteht ein reines Metallobjekt. Bei der Galvanotechnik hingegen bleibt das ursprüngliche Objekt erhalten und wird lediglich mit Metall überzogen.
Die Beschichtung kann aus verschiedenen Metallen bestehen, z. B. Kupfer, Nickel, Silber, Gold oder Chrom. Auch Kombinationen aus mehreren Metallen sind möglich, um spezifische Eigenschaften wie Korrosionsschutz, Leitfähigkeit oder Festigkeit zu erzielen.
Im Bereich 3D-Druck bedeutet das: Ein Kunststoffteil wird mit einer metallischen Schicht überzogen, was sowohl optische als auch mechanische Vorteile bringt.
Warum sollte man 3D-Drucke galvanisieren?
Die Kombination aus 3D-Druck und Galvanotechnik eröffnet einzigartige Vorteile. Kunststoffteile lassen sich schnell und günstig herstellen und durch eine galvanische Beschichtung mit den Eigenschaften von Metall aufwerten. So entstehen hybride Bauteile mit hoher Gestaltungsfreiheit, reduzierten Materialkosten und hervorragenden funktionalen Eigenschaften.
Vorteile auf einen Blick:
- Höhere Festigkeit und Zugbelastbarkeit durch metallische Außenhülle
- Schutz vor Umwelteinflüssen, z. B. Chemikalien, UV-Strahlung oder Feuchtigkeit
- Verbesserte elektrische Leitfähigkeit für Antennen, Kontakte oder Abschirmungen
- Wärmeleitfähigkeit – z. B. für LED-Halterungen oder Kühlkörper
- Ästhetische Aufwertung – metallische Oberflächen wirken hochwertig, können poliert oder strukturiert werden
- Korrosionsschutz – ideal für langlebige Außenanwendungen
Zudem lassen sich durch die Galvanotechnik von 3D-gedruckten Prototypen Bauteile erzeugen, die metallischen Produkten optisch und funktional sehr nahekommen. Diese 3D-Teile sind ideal für Tests, Designstudien oder Vorserienmodelle.
Welche Materialien lassen sich beim 3D-Druck galvanisieren?
Nicht jeder 3D-gedruckte Kunststoff ist sofort bereit für die Galvanik. Das Bauteil muss leitfähig sein, damit der elektrochemische Prozess funktioniert. Damit Sie die passenden Materialien für Ihren 3D-Druck einplanen, sollten Sie diese gängigsten Optionen kennen:
- ABS: Sehr gut geeignet, da es sich leicht chemisch beizen und aktivieren lässt.
- PLA und PETG: Weniger ideal, aber mit leitfähigem Lack (z. B. Graphit- oder Kupferlack) dennoch nutzbar.
- Harz (Resin): Bei SLA- und DLP-Drucken möglich, erfordert jedoch gute Nachbearbeitung.
- Nylon: Gute mechanische Eigenschaften, lässt sich galvanisieren, aber schwieriger zu beschichten.
Der Ablauf: Schritt für Schritt zum metallisierten 3D-Druckteil
Um ein 3D-Bauteil nach dem Druck mit der Galvanotechnik zu bearbeiten, sollten Sie den Ablauf kennen. Wichtig ist eine gute Vorbereitung. Das Teil wird gereinigt und eventuell geschliffen, um Unebenheiten zu entfernen. Denn diese können beim Galvanisieren ein Problem darstellen.
Sollten Sie einen nicht-leitfähigen Kunststoff verwendet haben, sollten Sie vor dem Galvanisieren einen leitfähigen Lack auftragen. Wie geht es dann weiter:
- Galvanikbad: Das Bauteil wird in eine Lösung mit Metallionen getaucht und mit Strom beaufschlagt.
- Abscheidung: Die Metallionen lagern sich gleichmäßig auf dem Bauteil ab.
- Nachbehandlung: Polieren, versiegeln oder weitere Beschichtungen (z. B. Verchromung).
DIY oder Dienstleister-was ist für Sie besser?
Für Hobbyanwender ist die Galvanotechnik prinzipiell auch von zu Hause aus umsetzbar. Es gibt Startersets für kleine Teile und Anleitungen online. Wichtig sind hier vor allem Sicherheitsvorkehrungen. Denn Strom, Chemikalien und Lösungen sind nicht ungefährlich.
Wer auf Nummer sicher gehen will oder eine professionelle Qualität benötigt, kann auch auf Dienstleister zurückgreifen. Diese bieten oft auch Beratung zur Materialwahl und Vorbehandlung an.
Anwendungsbeispiele für das Galvanisieren beim 3D-Druck
Die Galvanotechnik findet in vielen Branchen Anwendung. Eingesetzt wird es unter anderem beim Prototyping oder auch in der Serienfertigung. Überall da, wo flexible Bauteile mit metallischen Eigenschaften zum Einsatz kommen können, ist der 3D-Druck mit passender Galvanisierung ideal. Hier sind einige Anwendungsbeispiele:
- Luft- und Raumfahrt: Schutzschichten gegen Korrosion und Verschleiß bei hochbelasteten Verbindungselementen
- Automobilindustrie: Verchromte Stoßstangen, Zierleisten und Radkappen – teils aus 3D-Druck und Galvanik
- Medizin und Zahnmedizin: Korrosionsbeständige Instrumente oder Implantatteile
- Energietechnik: Leitfähige Oberflächen für Kontakte, Kabel, Antennen oder Solarzellen
- Funk- und Mikrowellen-Technik: Galvanisierte Antennen aus Kunststoff mit hohem Designspielraum
- Prototypenentwicklung: Schnelle, kostengünstige Herstellung funktionaler Einzelteile durch Kombination von SLA-Druck und Galvanik
Grenzen und Herausforderungen beim Galvanisieren
So vielseitig Galvanisierung auch ist, gibt es auch Herausforderungen und Grenzen beim Einsatz. Es gibt beispielsweise Sicherheitsrisiken. Der Umgang mit Strom und chemischen Lösungen wie Schwefelsäure oder Kupfersulfat ist nicht ungefährlich. Es besteht das Risiko von Verätzungen, Einatmen gefährlicher Dämpfe und elektrischer Schläge. Eine gute Belüftung, das Tragen von Schutzkleidung (Handschuhe, Schutzbrille, Maske) und ein sicherer Arbeitsplatz sind unerlässlich.
Hinzukommen technische Hürden. Kunststoffteile müssen zunächst leitfähig gemacht werden, meist durch das Auftragen spezieller leitfähiger Lacke (z. B. auf Graphit- oder Kupferbasis). Die Haftung dieser Schicht und ihre gleichmäßige Aufbringung sind entscheidend für das spätere Ergebnis.
Worauf sollten Sie noch achten:
- Komplexität bei Mehrschichtsystemen: Besonders bei funktionalen Teilen oder dekorativen Effekten werden häufig mehrere Metallschichten (z. B. Kupfer, dann Nickel, dann Chrom) nacheinander aufgebracht. Das erfordert exakte Prozesskontrolle hinsichtlich Stromstärke, Badzusammensetzung, Dauer und Temperatur. Schon kleine Abweichungen können zu schlechter Haftung oder ungleichmäßiger Schichtdicke führen.
- Kosten und Know-how: Zwar ist der Einstieg mit DIY-Mitteln möglich, doch für hochwertige, gleichmäßige Beschichtungen ist viel Erfahrung nötig. Professionelle Galvanikdienstleister arbeiten mit Industrieanlagen, können große oder komplexe Bauteile bearbeiten und erzielen reproduzierbare Ergebnisse. Der Aufbau einer eigenen Werkstatt ist aufwendig und lohnt sich meist nur bei regelmäßiger Anwendung.
- Umwelt- und Entsorgungsaspekte: Die eingesetzten Chemikalien müssen fachgerecht gelagert und entsorgt werden. Auch aus rechtlicher Sicht (z. B. Umweltauflagen) kann der Betrieb einer eigenen Galvanikanlage herausfordernd sein.
Trotz dieser Herausforderungen lohnt sich die Technik. Besonders bei Einzelstücken, kleinen Serien oder funktionalen Prototypen kann man dieses Verfahren empfehlen. Wer die Prozesse versteht oder auf erfahrene Partner zurückgreift, kann mit Galvanisierung beeindruckende Resultate erzielen.